The challenge:
unreliable production machinery
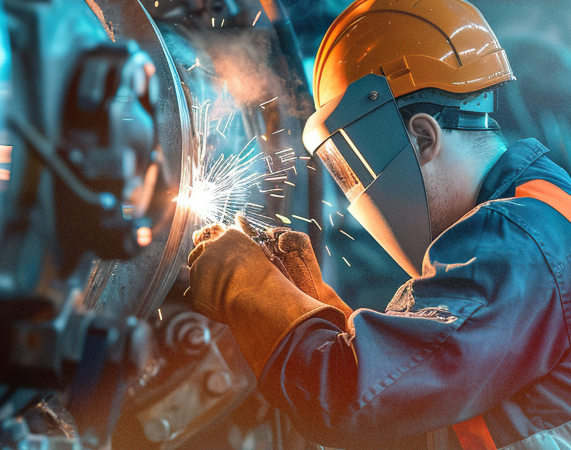
A mid-sized producer of precision-engineered components relied on a fleet of production machinery to meet high-volume orders.
As its equipment was long past its heyday, the company regularly experienced breakdowns, which disrupted operations, delayed delivery schedules, and increased repair costs.
The traditional maintenance approach—scheduled inspections and addressing failures when they occurred—was inefficient and resulted in costly unplanned downtime.
With growing customer demand and tight production deadlines, the company sought a smarter way to maintain the health of production machinery and minimise disruptions.
Assessing available solutions
#1 The first line of inquiry involved manually logging performance data and conducting regular inspections.
While this provided some insights, it was labour-intensive, prone to human error, and lacked predictive capabilities.
#2 The company also considered advanced diagnostics tools,
which offered real-time performance data but failed to predict future issues.
#3 Another option was to outsource maintenance tasks to third-party experts,
but the costs were impractical for a facility with diverse machinery. Besides, company leaders were ready to invest in long-term solutions that would gradually automate maintenance processes.
#4 That’s why, finally, the manufacturer turned to IoT technologies and predictive analytics,
which promised real-time production machinery monitoring, pattern analysis, and anticipating potential failures.
However, having a limited budget and technical expertise, the company required support in managing the deployment of new tools for maximum impact.
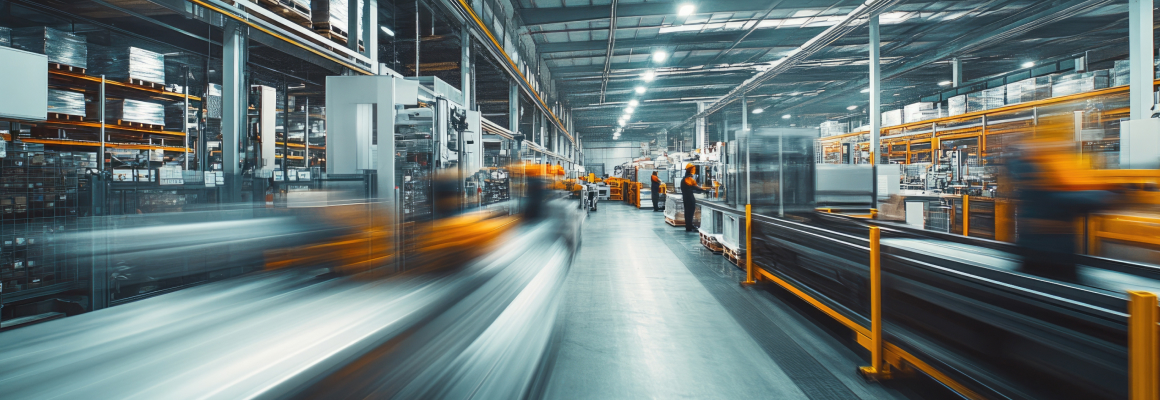
The winning solution:
IoT-enabled production machinery maintenance
-
The company enlisted an experienced technology partner
who helped them plan the integration of predictive maintenance solutions. External specialists analysed the challenge and suggested a tiered approach to implementing new technologies.
-
The company started by installing IoT-connected sensors on the most critical production machines,
which provided valuable performance data. The team quickly started tracking essential metrics such as temperature, vibration, and operating speed thanks to cloud-based analytics.
-
This data is continuously transmitted to a central analytics platform,
where ML algorithms identify patterns and deviations indicative of wear and tear or impending failures.
-
Key features of the solution include:
- Real-time alerts for anomalies.
- Predictive insights to anticipate failures before they take place.
- Comprehensive reporting on equipment health to guide decision-making.
The system seamlessly integrates with the company’s existing software, enabling automatic scheduling, resource allocation, and sending alerts and updates to production machinery operators.
Results and plans
A01
The solution delivered impressive results within the first year.
Unpredicted downtime due to machinery failures dropped by 35%, while targeted servicing decreased maintenance costs by 20%.
A02
With increased uptime, the company experienced improved productivity and met growing customer demands without delays.
This success wouldn’t have been possible without the tiered approach and agile project management provided by the external technology partner.
A03
The company plans to expand the system to more production lines and integrate additional data sources,
such as environmental conditions, for even more accurate predictions. The team is also exploring AI-powered optimisation tools to balance equipment usage, ensure even wear, and prolong the life of its production machinery.
A04
This use case demonstrates the power of IoT and analytics for manufacturing operations, boosting efficiency and driving costs down.
It also proves how much of a difference the right technology partner can make, especially if you’re only starting your company’s digital transformation journey.