The challenge:
inefficient warehouse management system
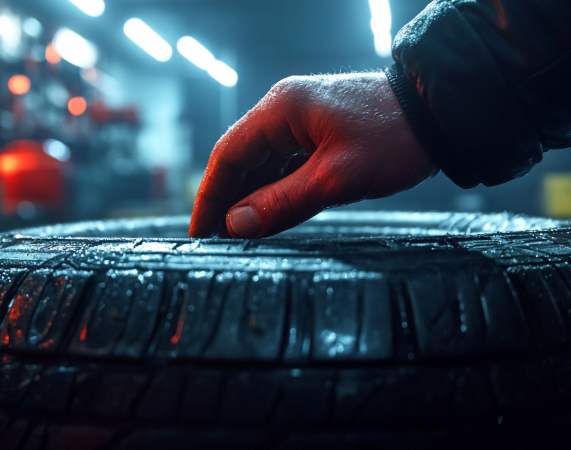
In large-scale warehousing operations, tracking vehicles and equipment is crucial for maintaining smooth workflows and meeting tight delivery deadlines.
Managing over 50 distribution centres across the UK, this logistics company faced significant issues locating and managing equipment within their sprawling warehouses.
Forklifts, pallet movers, and other machinery were often misplaced or underutilised, leading to delays and occasional bottlenecks. Additionally, manual tracking methods were time-consuming and prone to errors, negatively impacting productivity and resource allocation.
The company knew it needed to create a new, more efficient warehouse management system.
Evaluating available options
#1 Initial attempts to address the issue included temporarily assigning additional staff members to track assets manually and marking locations on warehouse maps.
However, these methods were too laborious and offered limited accuracy in real-time operations.
#2 The company considered using GPS trackers for vehicle tracking,
but their performance was subpar in indoor environments.
#3 Finally, the team assessed RFID and IoT-based solutions,
but the challenge lay in implementing these systems across the company’s diverse and extensive infrastructure.
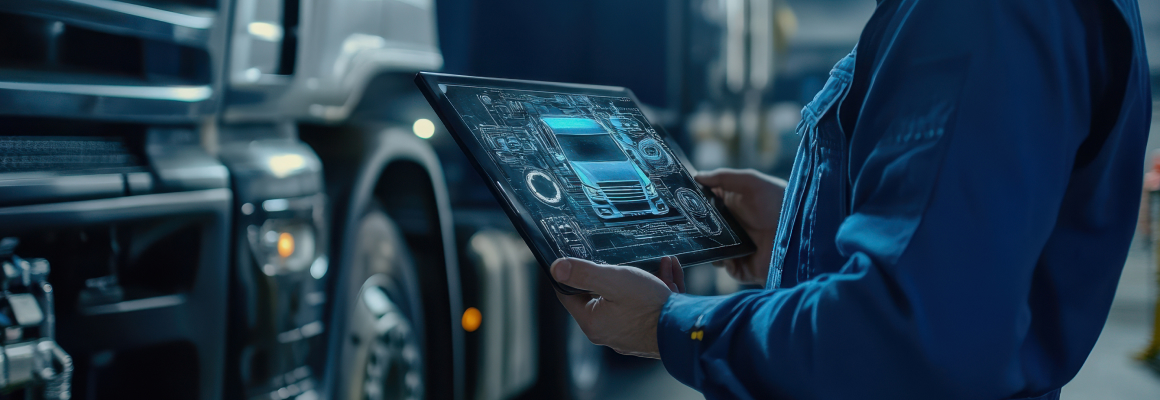
The winning solution:
IoT + RFID + ML for smart warehouse management
The company decided to combine the power of RFID tags and IoT sensors and include them in the first step of creating a more reliable warehouse management system.
The team added RFID tags to all equipment and placed sensors across vehicles, creating a robust tracking network. Once integrated with the existing warehouse management software, the system became a central space for real-time equipment location updates and usage data.
By collecting data from sensors and RFID tags and analysing it with ML models, the company can anticipate increased demand and optimise equipment usage to avoid bottlenecks.
Key features of the solution included:
-
Precise indoor tracking of vehicles and equipment.
-
Alerts for misplaced or inactive machinery.
-
Historical data analysis for optimised equipment usage.
-
Predictive analytics for anticipating periods of increased equipment demand.
-
The integration enabled warehouse operators to locate assets and streamline workflows quickly.
Results & plans: expandable warehouse management system
A01
The new warehouse management system reduced equipment search times by 40%, improving operational efficiency.
A02
Resource utilisation increased significantly as managers gained the ability to track and allocate equipment dynamically.
Reducing workflow bottlenecks translated to faster loading and unloading times, ultimately enhancing operations and the company’s bottom line.
A03
Building on this success, the team plans to extend its warehouse management system
to additional loading areas and integrate predictive maintenance to schedule repairs.