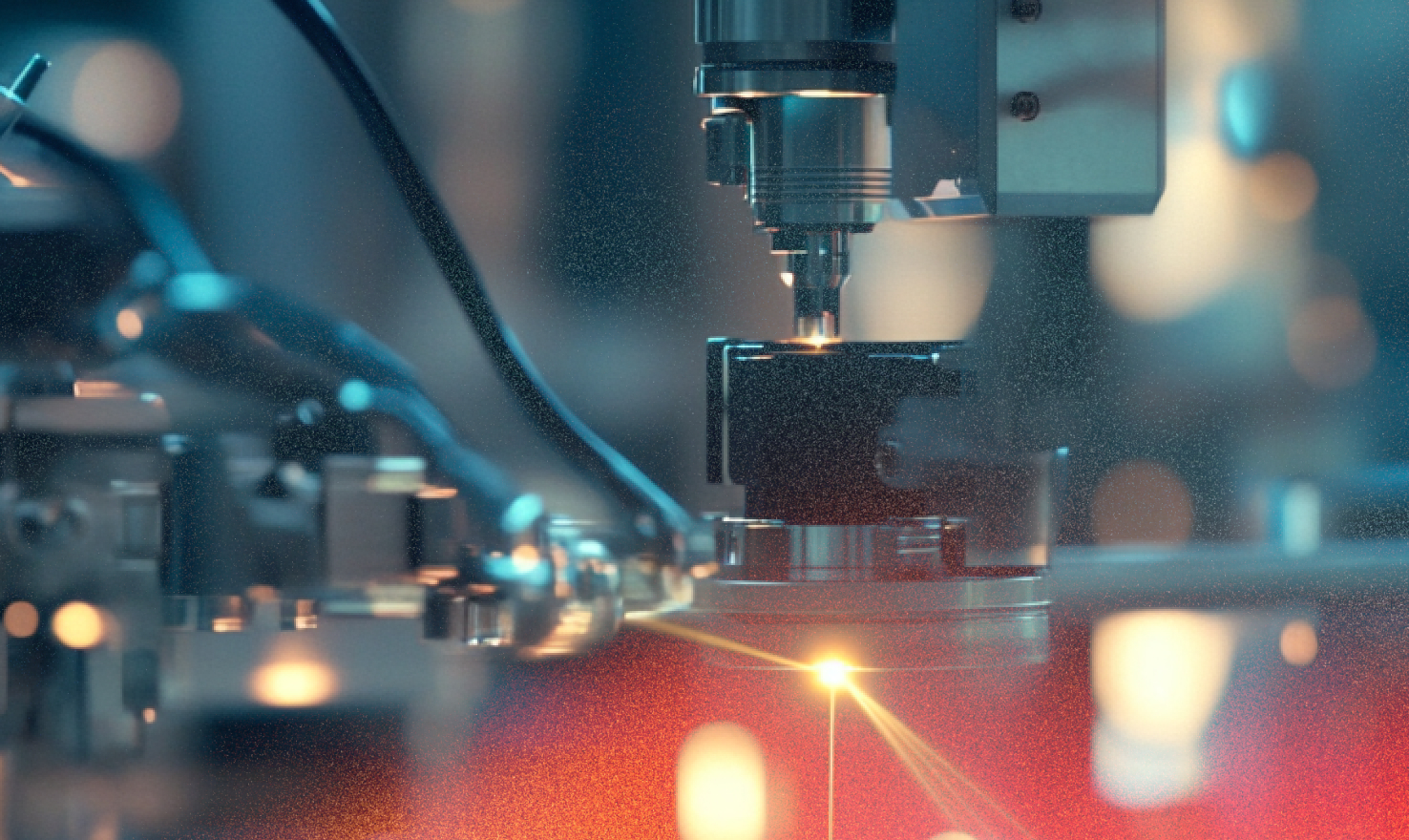
IoT
Industrial IoT & Cloud Computing: What You Need to Know to Get Started
Imagine a factory where machines predict their failures, production lines run autonomously, and errors are almost non-existent. This vision is the promise of Industrial IoT.
And it’s becoming real, as Statista predicts that the number of IoT-connected devices will exceed 20 billion by the end of 2025 and double by 2033.
This growth isn’t surprising, as the Internet of Things’ potential applications are vast, and so is its impact across many sectors. When speaking of IoT in manufacturing, it makes sense to refer to its specific subset—Industrial IoT (IIoT)—one of the enablers of Industry 4.0.
In this article, we’ll cover how Industrial IoT differs from other IoT types, its benefits, how cloud computing unlocks them, and the challenges you must account for. Read on!
What is Industrial IoT?
IIoT refers to the use of IoT in production and manufacturing settings, especially for instrumentation and control of sensors and devices. This ability lets companies monitor and manage assets remotely and continuously use sensor data.
Popular Industrial IoT applications include:
– Real-time production-line monitoring and optimisation
Sensors attached to equipment provide continuous data on production workflows. Manufacturers can analyse and use that input to spot bottlenecks and areas for improvement.
– Predictive maintenance
Industrial IoT devices allow manufacturers to consistently monitor their equipment’s condition to create a baseline and predict issues before they occur.
Learn more about PdM in this article.
– Production quality assurance
Connected devices monitor real-time production processes, identify anomalies, and provide insights for timely corrective action.
The difference between IoT and Industrial IoT
While both IoT and IIoT use interconnected devices and sensors, the distinction between them lies primarily in their focus, scale, and requirements.
While IoT encompasses multiple consumer applications, such as smart homes, IIoT focuses specifically on industrial use cases like improving manufacturing supply chains.
Industrial IoT typically requires higher levels of security, precision, and interoperability, as it often involves critical systems where downtime is costly. In contrast, consumer IoT targets individual users, focuses on convenience, and has less stringent reliability requirements.
Key benefits of Industrial IoT
#1: Optimised production processes and costs
Industrial IoT automates workflows, improving efficiency and reducing costs. By analysing real-time data from equipment, manufacturers can optimise entire production lines, not just individual machines.
For example, Harley-Davidson’s IoT-enabled factory reduced production time from 21 days to 6 hours, saving $200 million annually.
#2: Shorter Time-to-Market
More efficient operations and increased flexibility translate to shorter production cycles and faster delivery of new products to the market.
Industrial IoT tools enable faster decision-making in response to market changes and emerging trends – and today’s customers increasingly expect quick turnaround times.
The growth of on-demand manufacturing directly responds to this need, and it wouldn’t be as fast without IoT and AI.
#3: Improved safety
IoT sensors monitor the workplace and improve employee safety on the floor, production line, and distribution.
Production teams are immediately alerted in case of accidents, and operations cease until the issue is resolved. Incident logs can generate valuable data for IIoT systems to feed on and help prevent similar occurrences in the future.
For instance, the Australian company EMS uses IoT for fuel leak detection and prevention and quickly achieved a 500% ROI on the implementation. Thanks to the proactive management of petrol stations, EMS also significantly reduced safety and environmental risks.
#4: Fewer errors
The human factor is the most significant risk regarding the security and production quality. By automating manual production workflows, manufacturers reduce the odds of human error.
For example, thanks to an IoT platform, US manufacturer Fastenal experienced an 11% increase in machine utilisation and 150,000 more parts produced in the first three months.
#5: Digital twins
A digital twin is a virtual duplicate of physical objects created with Industrial IoT, cloud computing, and AI. Such digital replicas help managers simulate processes, run tests, and identify problems remotely.
For example, Siemens uses digital twins to create a virtual replica of the entire production process at the Amberg plant. The technology quickly brought significant results, such as a 20% boost in productivity and a 40% enhancement in space efficiency.
Let’s now shed light on the role of the Industrial IoT’s leading enabler – the cloud.
Why cloud computing is the IIoT’s backbone
IoT sensors generate large volumes of data, which require storage and processing to bring business value—this is where cloud computing comes in.
The cloud provides the structure and tools to store and analyse industrial data. It’s the backbone of industrial IoT platforms, enabling connectivity and providing the computational power for data analytics and ML algorithms to extract insights.
IIoT services are now available from all the major cloud service providers: AWS, Google Cloud, and Microsoft Azure.
Common challenges of IIoT in the cloud
Despite the numerous benefits of Industrial IoT in the cloud, there are also several challenges:
#1: Data and system security
Unencrypted data transmission from IIoT devices to the cloud is vulnerable to interception, potentially exposing sensitive manufacturing information.
To give an example of scale, only in the first half of 2021 did security service provider Kaspersky track over 1.5 billion IoT breaches. Most attackers brokered access to IoT networks via the telnet protocol, a CLI that enables remote communication with a device or server.
With a far more diversified attack surface, ensuring security is undoubtedly a top priority for Industrial IoT systems.
#2: Interoperability issues
– Data integration
Integrating data from Industrial IoT with existing systems like ERPs and databases is often challenging.
– Connectivity
IIoT often also proves problematic in terms of connectivity. According to McKinsey, organisations must account for the range, number of locations (i.e., multiple sites and factories), and power consumption when connecting industrial IoT systems.
– Legacy system compatibility
Many industrial devices were not designed for connecting to the cloud. They lack advanced security features and potentially introduce vulnerabilities when connected to modern cloud systems.
There is no one set of standards for processing data between devices or securing systems with equipment that was never meant to be “smart”—it all requires individual consideration.
And that asks for time and expertise, bringing us to another common IIoT issue.
#3: Skills gap
Companies often lack internal expertise in managing and securing Industrial IoT systems in the cloud. This situation prevents them from fully developing Industrial IoT systems and taking advantage of more advanced solutions.
Seeking support and training for your staff is always a step in the right direction. You could consider the following:
- Enlist external IoT development consultants;
- Use online training platforms like Coursera or Udemy to upskill your workforce in industrial IoT management;
- Consider partnering with a vendor specialised in your field.
With emerging trends like 5G connectivity, edge computing, and advanced AI algorithms, this gap will only grow larger, so now is the right time to act.
Over to you
Industrial IoT greatly benefits manufacturers. From real-time monitoring and enabling predictive maintenance, IIoT can enhance quality control, optimise efficiency, shorten Time-to-Market (TTM), and improve safety.
These advantages wouldn’t be possible without the cloud. Combined with the right cloud services, AI, and data analytics tools, Industrial IoT truly unlocks innovation.
However, these opportunities come at a price of potential issues such as data security integration and interoperability. With Industrial IoT’s complexity, a lot can go wrong if you lack the necessary knowledge.
Don’t go it alone; we’re here to help. Contact us, and let’s explore how Industrial IoT can transform your manufacturing processes to help your business thrive.